Exploring the Inner Workings of Truck Mounted Crane Parts
Introduction
Truck mounted cranes are invaluable pieces of equipment in various industries such as construction, transportation, and logistics. These powerful machines are capable of lifting and moving heavy loads with precision and efficiency. To understand how truck mounted cranes operate, it is essential to delve into the intricate details of their parts and components. In this comprehensive guide, we will explore the various components that make up a truck mounted crane and discuss their functions, importance, and maintenance requirements.
1. Boom Assembly
One of the most critical components of a truck mounted crane is the boom assembly. The boom is the long, extendable arm of the crane that is used to lift and move heavy objects. It can be made of steel or aluminum and is designed to withstand the immense stress and weight placed on it during operation. The boom assembly consists of several key parts, including the boom sections, boom extension mechanism, and boom support system.
1.1 Boom Sections
The boom of a truck mounted crane is typically composed of multiple sections that can be extended or retracted to reach different heights. These sections are connected by hydraulic cylinders that allow for smooth and controlled extension and retraction. The number of boom sections and their length vary depending on the crane model and lifting capacity. Proper maintenance and inspection of the boom sections are crucial to ensure safe and efficient crane operation.
1.2 Boom Extension Mechanism
The boom extension mechanism is responsible for extending and retracting the boom sections to reach the desired lifting height. It is typically powered by hydraulic cylinders that provide the necessary force to extend or retract the boom. The extension mechanism is controlled by the crane operator using a series of hydraulic valves and controls located in the crane cabin. Regular inspection and maintenance of the boom extension mechanism are essential to prevent malfunctions and ensure smooth operation.
1.3 Boom Support System
To support the weight of the boom and the loads it lifts, truck mounted cranes are equipped with a robust support system. This system includes outriggers, stabilizers, and counterweights that help stabilize the crane during lifting operations. Outriggers are extendable legs that provide additional support and prevent the crane from tipping over. Stabilizers are hydraulic devices that help level the crane on uneven terrain, while counterweights are added to the rear of the crane to balance the weight of the lifted load. Proper deployment and use of the boom support system are crucial for safe and efficient crane operation.
2. Hydraulic System
The hydraulic system is the heart of a truck mounted crane, providing the power and control needed to lift and move heavy loads. Hydraulic systems use fluid pressure to generate force and motion, making them ideal for heavy-duty applications such as crane operation. The hydraulic system of a truck mounted crane consists of several key components, including hydraulic pumps, cylinders, valves, and hoses.
2.1 Hydraulic Pumps
Hydraulic pumps are responsible for generating the fluid pressure needed to operate the crane's hydraulic system. These pumps are typically driven by the crane's engine and can be of various types, such as gear pumps, vane pumps, or piston pumps. The type and size of the hydraulic pump depend on the crane's lifting capacity and hydraulic power requirements. Regular maintenance and inspection of hydraulic pumps are essential to prevent leaks, malfunctions, and system failures.
2.2 Hydraulic Cylinders
Hydraulic cylinders are essential components of the crane's hydraulic system, responsible for converting fluid pressure into linear motion. These cylinders are used to extend and retract the boom, operate the stabilizers and outriggers, and control other crane functions. Proper maintenance of hydraulic cylinders, including inspection for leaks, wear, and damage, is crucial to ensure the safe and efficient operation of the crane.
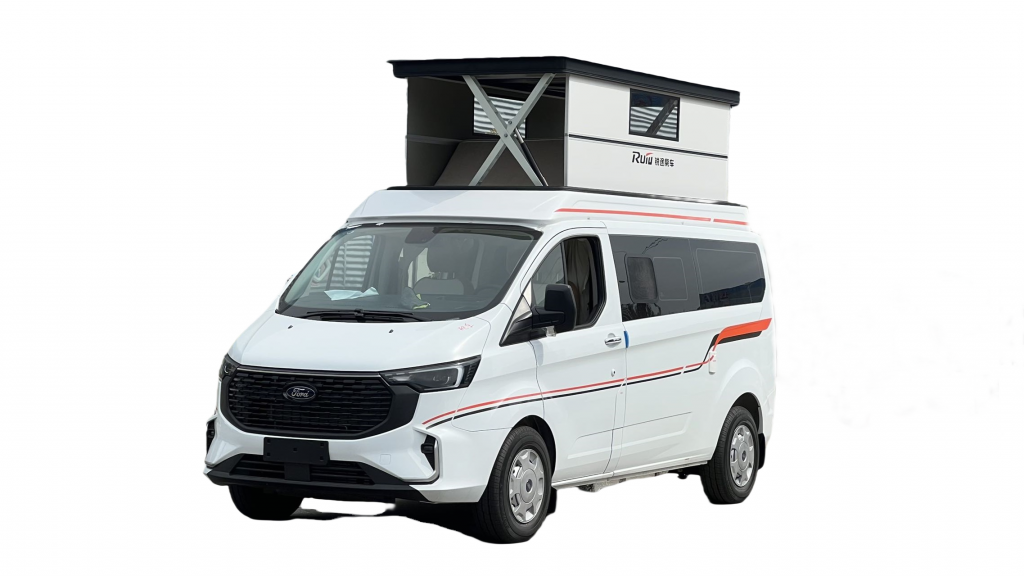
2.3 Hydraulic Valves
Hydraulic valves are used to control the flow and direction of hydraulic fluid within the crane's hydraulic system. These valves are operated by the crane operator using hydraulic controls in the cabin. Directional control valves determine the direction of hydraulic fluid flow, while pressure control valves regulate the pressure within the system. Regular inspection and maintenance of hydraulic valves are essential to prevent system malfunctions and ensure precise control of crane operations.
2.4 Hydraulic Hoses
Hydraulic hoses are used to transport hydraulic fluid between the various components of the crane's hydraulic system. These hoses are subject to high pressure and mechanical stress during operation, making them prone to wear, leaks, and damage. Regular inspection and replacement of hydraulic hoses are essential to prevent hydraulic fluid leaks, system malfunctions, and potential hazards to crane operators and bystanders.
3. Control System
The control system of a truck mounted crane is responsible for providing the crane operator with the means to operate and control the crane's various functions. Modern crane control systems are typically electronic or computerized, offering precise control and monitoring capabilities. The control system consists of control panels, joysticks, displays, sensors, and safety features that ensure safe and efficient crane operation.
3.1 Control Panels
Control panels are located in the crane cabin and provide the crane operator with access to the crane's controls and functions. These panels contain switches, buttons, and indicators that allow the operator to extend and retract the boom, operate the stabilizers and outriggers, and control other crane functions. Control panels are designed for ease of use and are typically ergonomically positioned for the operator's convenience.
3.2 Joysticks
Joysticks are commonly used in modern crane control systems to provide intuitive and precise control over the crane's movements. These joysticks allow the operator to control the direction, speed, and extent of the crane's movements with precision. Joysticks are often equipped with safety features such as deadman switches that prevent accidental operation and enhance operator safety.
3.3 Displays
Displays are used to provide the crane operator with real-time information about the crane's status, including boom position, load weight, hydraulic pressure, and system alerts. These displays are typically mounted in the crane cabin and are designed to be easy to read and interpret. Advanced displays may include touchscreen interfaces, diagnostic capabilities, and remote monitoring features for enhanced control and safety.
3.4 Sensors
Sensors are used throughout the crane to monitor various parameters such as load weight, boom position, hydraulic pressure, and system temperature. These sensors provide real-time feedback to the control system, allowing the operator to make informed decisions and adjustments during crane operation. Sensors play a crucial role in ensuring the safety and efficiency of crane operations by detecting potential issues and alerting the operator to take corrective action.
3.5 Safety Features
Safety features are integrated into the crane control system to prevent accidents, protect the crane operator, and ensure safe operation. These features may include overload protection systems, emergency stop buttons, automatic leveling controls, and alarms for low hydraulic pressure or system malfunctions. Safety features are designed to comply with industry standards and regulations to minimize risks and hazards associated with crane operation.
4. Structural Components
In addition to the essential functional components of a truck mounted crane, several structural components contribute to the crane's overall stability, strength, and durability. These components include the chassis, frame, outriggers, and counterweights, which work together to support the crane's weight and the loads it lifts.
4.1 Chassis
The chassis of a truck mounted crane forms the foundation of the crane and provides the structural support needed to carry the crane's components and the lifted loads. The chassis is typically a heavy-duty frame made of steel or aluminum that is mounted on the truck's suspension system. The chassis must be designed to withstand the dynamic forces and stresses encountered during crane operation, including acceleration, braking, and lifting.
4.2 Frame
The frame of a truck mounted crane supports the boom assembly, hydraulic system, and control system, ensuring their stability and alignment during operation. The frame is typically welded or bolted to the chassis and is designed to distribute the weight of the crane and the loads it lifts evenly. Proper maintenance of the frame, including inspection for cracks, corrosion, and fatigue, is essential to prevent structural failures and ensure the crane's longevity.
4.3 Outriggers
Outriggers are extendable legs that provide additional support and stability to the crane during lifting operations. These outriggers are deployed to the ground before lifting to prevent the crane from tipping over or becoming unstable. Outriggers are typically controlled hydraulically and feature adjustable pads or feet to accommodate different terrain conditions. Proper deployment and use of outriggers are crucial for safe and efficient crane operation.
4.4 Counterweights
Counterweights are added to the rear of the crane to balance the weight of the lifted load and prevent the crane from tipping forward. These counterweights are typically made of steel or concrete and are attached to the crane's frame or chassis. The amount of counterweight required depends on the crane's lifting capacity and the weight of the loads being lifted. Proper placement and adjustment of counterweights are essential for safe and stable crane operation.
5. Maintenance and Inspection
Regular maintenance and inspection of truck mounted crane parts are essential to ensure safe and efficient crane operation. Proper maintenance practices help prevent malfunctions, extend the crane's lifespan, and minimize downtime. Maintenance tasks may include lubrication, cleaning, inspection, adjustment, and replacement of worn or damaged parts. Sweeper trucks GPS tracking should be conducted by qualified technicians and in accordance with the manufacturer's guidelines and industry standards.
5.1 Lubrication
Proper lubrication of moving parts such as boom sections, hydraulic cylinders, and bearings is essential to reduce friction, wear, and corrosion. Lubrication helps maintain the smooth operation of the crane and prolong the lifespan of critical components. The type and frequency of lubrication depend on the crane model, operating conditions, and manufacturer's recommendations. Regular lubrication schedules should be established and followed to ensure optimal crane performance.
5.2 Cleaning
Regular cleaning of the crane's components helps prevent the buildup of dirt, debris, and contaminants that can affect the crane's operation and performance. Cleaning should be done using appropriate cleaning agents and methods to avoid damage to sensitive components. Special attention should be paid to hydraulic hoses, filters, and electrical connections to ensure they remain free of obstruction and contamination. Cleanliness is essential for safe and efficient crane operation.
5.3 Inspection
Routine inspections of truck mounted crane parts are crucial to detect potential issues, wear, and damage before they escalate into major problems. Inspections should be conducted by trained technicians who are familiar with the crane's components and operation. Visual inspections, functional tests, and diagnostic procedures should be performed regularly to ensure the crane's safety and reliability. Any signs of wear, leaks, or malfunctions should be addressed promptly to prevent accidents and downtime.
5.4 Adjustment
Regular adjustment of crane components such as hydraulic systems, control systems, and structural elements is necessary to maintain optimal performance and safety. Hydraulic systems may require adjustment of pressure settings, valve settings, or cylinder positions to ensure proper operation. Control systems may need calibration or programming updates to maintain accuracy and responsiveness. Structural components may require alignment, tightening, or reinforcement to prevent structural failures.
5.5 Replacement
Over time, truck mounted crane parts may wear out, become damaged, or reach the end of their service life, requiring replacement. Components such as hydraulic hoses, seals, bearings, and electrical parts may need to be replaced periodically to ensure the crane's reliability and safety. Replacement parts should meet the manufacturer's specifications and quality standards to maintain the crane's performance and compliance with industry regulations. Proper installation and testing of replacement parts are essential to ensure their effectiveness and reliability.
Conclusion
Truck mounted cranes are complex machines that rely on a multitude of parts and components to perform their lifting and moving tasks. Understanding the inner workings of truck mounted crane parts is essential for safe and efficient crane operation. Components such as the boom assembly, hydraulic system, control system, and structural elements work together to provide the power, control, and stability needed to lift heavy loads with precision and accuracy. By following proper maintenance and inspection practices, crane operators can ensure the longevity, reliability, and safety of their truck mounted cranes.